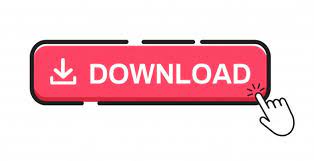

Spiral roughing uses a helical toolpath that maintains a more constant load on the cutter and machine tool With FeatureCAM 2012 it is now possible to do this without having to offset the driving curves. With a G71 move, it’s not possible to zero out a part as a finishing pass as an over stock for the finishing pass needs to be left. One is the added support for a machining stock. There are some pretty specific turning updates. This constant tool loading means less stress on the cutter and machine tool. Whereas previous releases used a concentric circular path with link, the system now uses the same method as PowerMill and creates these tool-paths using a helix into the material. In terms of machining operation updates, enhancements have been made to spiral roughing on 3D surface models. Using the tools within FeatureCAM, the process of inserting the cutter into a hole, positioning it, cutting the required feature and then retracting it, can all be done in a single operation. This typically requires a part to be re-fixtured, but many machinists avoid this by using the combination of a controller specific operation (such as a G87 on a Fanuc control) and an I-shaped cutter. In previous releases, these two key values would be driven purely by the material (such as 10% step-over for aluminium), but this can now be adapted to a percentage of the cutter length as well and by operation type.įeatureCAM can now program back boring operations, allowing more parts to be complete in a single setupĪnother area is back boring or trepanning. Step-overs and step-downs are now more flexible. There are new technical updates intended to take the pain out of the NC programming process.
#FEATURE CAM PRICE WINDOWS#
For example, features and operations can now be multi-selected using the standard Windows keyboard modifiers and it also works with standard cut/copy/paste keys. It has also been made more accessible for the casual user. This makes the whole system more efficient, particularly when working with large and complex datasets. Instead of introducing such tools to FeatureCAM, the goal has been to make it easier to use, especially for the casual user.Ī good example is how workflow has been enhanced with the use of hotkeys to expose more functions. The key difference is that with PowerMill users can continue to dive in and tweak each option and each parameter to match their requirements. For FeatureCAM 2012, Delcam claims that the operation and machining strategies between PowerMill and FeatureCAM are now comparable.
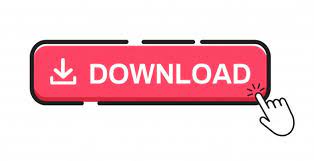